View our Potash Webinar Series for more information about this topic and more.
Saskatchewan produces over 30 per cent of the world’s potash, which is extracted using either conventional mining or solution mining techniques from subsurface deposits that are at least 1,000 metres deep. Solution mining is generally favourable when ore is deeper than 1,000 meters underground and where the depth, rock solubility, mineralogy and sedimentary structures make conventional mining riskier and less economic.
This process involves dissolving water-soluble potash ores with a heated brine solution. The dissolved salts are then pumped out of the cavern to the surface, where the water is evaporated and the remaining minerals are recovered.
Solution mining has advantages over conventional techniques, however, there are technical challenges associated with the extraction process. While both conventional and solution mining require detailed knowledge of the formation, only conventional mining has direct access to the underground potash bed to help understand the geology.
Relying on selective brine dissolution, solution mining’s effectiveness is largely determined by mineral solubility and saturation rates resulting from factors such as potash bed mineralogy, heated brine-potash geochemistry and thermodynamics. Important parameters for the engineering design of the solution mining process are acquired from laboratory-scale brine injection tests on representative potash cores, which can be conducted together with other core characterization and water chemistry analysis techniques.
creating field conditions in the lab
Designing these experimental studies can be complex as many factors need to be considered, such as preserving and preparing mineral samples, stress conditions, scaling the flow rate and residence time, and data collection throughout the test duration.
For over 30 years, SRC has worked with oil industry clients to understand in-situ recovery processes in deep petroleum reservoirs. Our experts use specialized equipment to re-create the temperature and pressure conditions that exist in the underground deposits to study in-situ flow, dissolution and precipitation, while keeping the rock sample under realistic overburden pressure conditions.
Cores about 2-10 cm in diameter wide are placed in special sleeves and then into a pressurized vessel. Once the model is prepared, we can study the in-situ leaching process. From this data, we can build analytical and numerical models of the process.
ct scanning for solution mining
We can monitor the dissolution process using high-resolution X-ray computed tomography (CT). For the mining industry, the scanned 3-D imagery data can show internal microscopic features of core samples, such as grain size and shape, pore size and network, lithology and mineralogy, and in-situ fluids distribution, before and after the leaching process. This capability makes CT scanning a perfect non-destructive technique (NDT) for tackling potash solution mining tests.
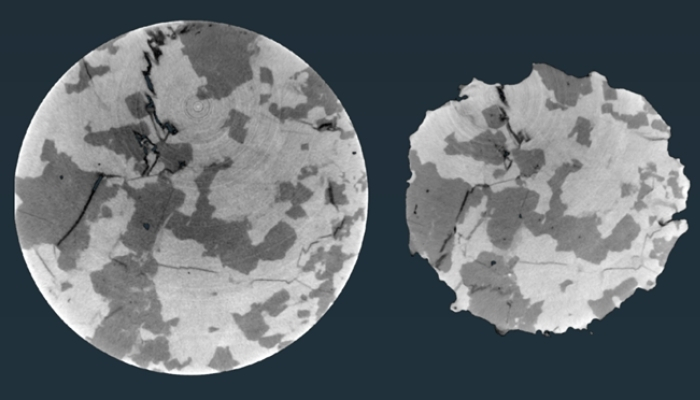
Our advanced industrial CT scanner is equipped with both a 450-kV mini-tube and a 225-kV micro-tube. These are a lot more powerful compared to a typical medical CT scanner (typically less than 100 kV). The high energy 45- kV mini-tube is used to scan high-density or thick material, such as the high-pressure coreholder or full-sized core samples. The 225-kV micro-tube can achieve a high resolution that allows for the identification of small samples, such as mineral grains, pore space and fluid phases.
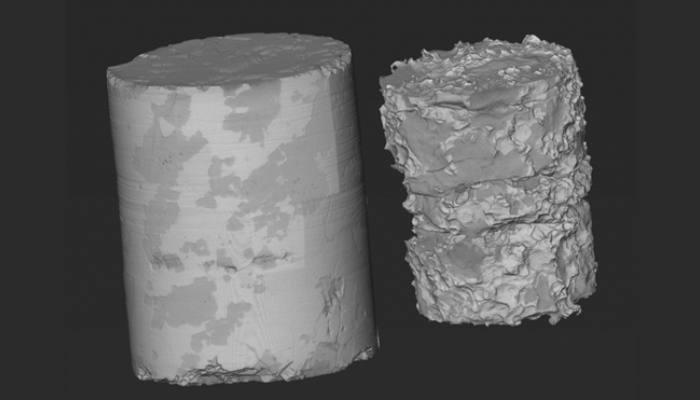
The main advantage of a CT scanner is its non-destructive testing nature. We can investigate a core's interior without damaging the sample. For a brine injection test in potash core, CT scanning makes it possible to identify brine flow channels in the pore space, and where and how quickly the mineral phases are dissolved (as shown in the images in this post).
The better we can understand these mechanisms, the more we can help mining operations predict recovery and optimize flow patterns to enhance recoveries.
This article first appeared in PotashWorks.