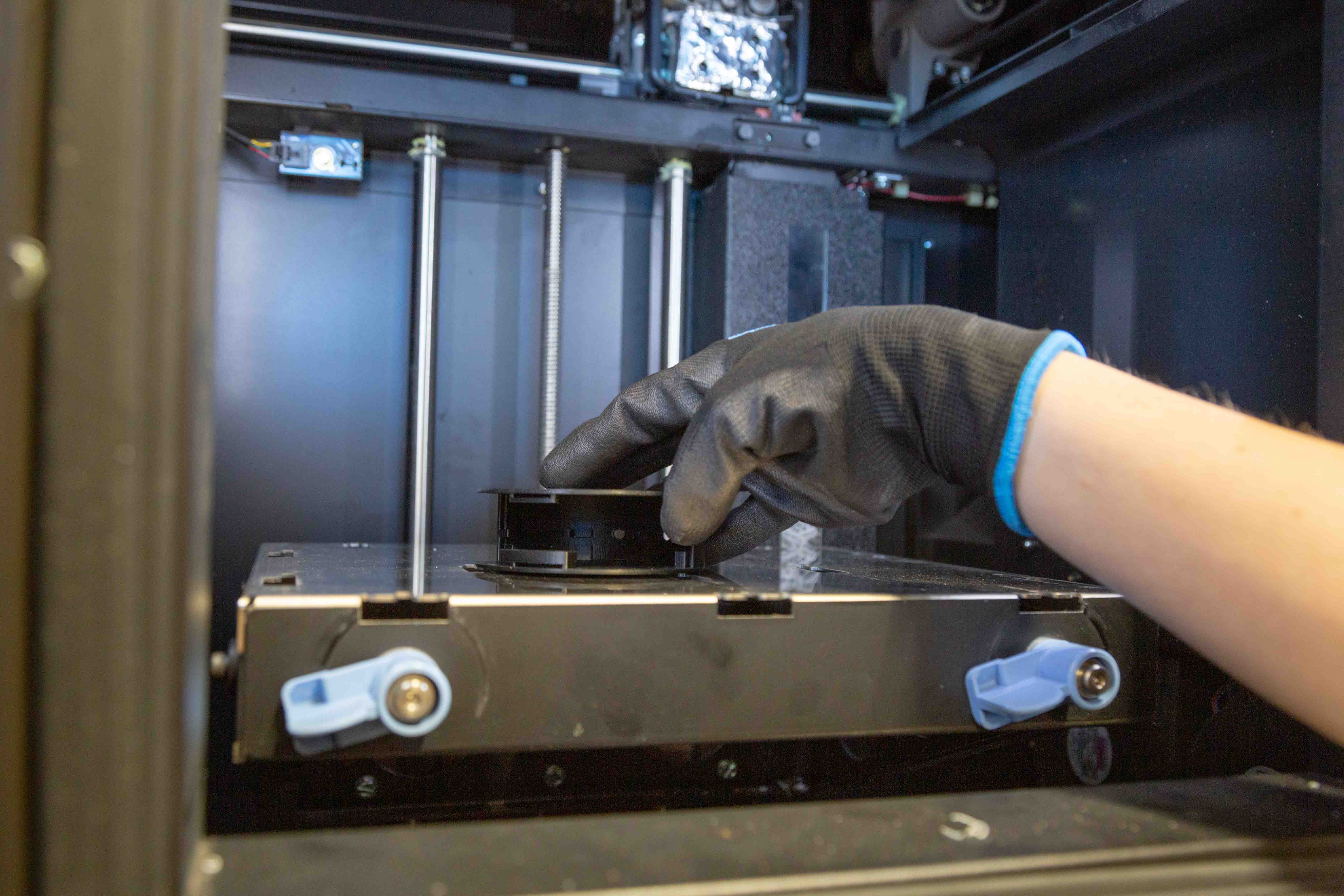
This is a contributed blog post written by former SRC employee, Andy Goodson.
You may be familiar with the gadgets and trinkets a home 3-D printer can produce, but engineering 3-D printed parts for industry is a different game. With strength and stiffness requirements, load-carrying parts and mechanical components are slow to find their way to critical applications.
Additive manufacturing is a 3-D printing technique that produces parts inherently different from the inside out when compared to conventional manufacturing. To address the challenges this poses, SRC’s Industrial Engineering team has devised ways to help industry adopt additive-manufactured parts. The challenge for engineers is building parts with the best possible strength-to-weight and stiffness-to-weight ratios, ensuring they meet the standards of industrial use.
Engineers are free to design and create things using additive manufacturing that were once impractical or even impossible to build using typical methods. It can drastically reduce the weight, total part count and cost of manufactured parts, while being more efficient and intricately complex. To do this reliably, however, requires specialized tools, software and know-how.
How does additive manufacturing differ from other techniques?
As the name implies, additive manufacturing is a process of adding material layer by layer. This contrasts with subtractive manufacturing, which is essentially like sculpting the desired part out of a block of solid material, or formative manufacturing, which shapes objects by applying heat and pressure or by pouring melted material into a casting mold and letting it solidify.
By nature, most 3-D printed parts are anisotropic, meaning their strength and mechanical properties depend on the direction they’re built or layered. We may think of them like sedimentary rocks, such as shale and sandstone, which are formed when silt and sand are layered and compressed over time. These rocks are like a firmly packed deck of cards, which is stronger and more uniform in one direction, but may deform or slide apart more easily in another.
Subtractive and formative manufacturing, on the other hand, use or produce materials that are relatively isotropic, meaning their physical properties are roughly the same in all directions—like sculptures from solid rock.
This does not mean anisotropic materials are inherently weaker, but more design expertise is required to build parts for practical use. There are advantages and constraints to each method of 3-D printing. Properties such as impact energy and fatigue strength may differ significantly from conventionally manufactured parts, and engineers must mitigate any material imperfections that may exist from the 3-D printing process.
Whether a manufacturer chooses an additive technique depends on factors such as the size of the production run, cost and type of building materials. While additive manufacturing is impractical for high-volume production runs (where casting makes more sense), it excels in its own niche: rapid prototyping and manufacturing short runs of strong, lightweight custom parts.
Why is optimization important for 3-D printed parts?
Although additive manufacturing offers design freedom, it’s critical the parts can do their job as good as or better than those made by conventional methods. Design optimization is required to fully exploit the additive technique.
Engineers have historically been limited to standardized shapes and designs of conventional manufacturing methods. Sheldon Hill, manager of SRC’s Industrial Engineering team, explains: “Engineers are largely constrained in the design process to simple beams, plates, and in the most complex cases, trusses. You end up with a limited number of shapes and structures you can deal with. We want to give the engineer more flexibility in designing things.”
Designing complex organic shapes, without casting, frees engineers to reimagine and transform structural parts essentially from scratch. In doing so, they can trim all excess material.
Optimization means getting more out of less. When you remove the non-stress bearing material of a bracket, for example, the resulting piece has a higher strength-to-weight ratio and serves the same function, but with less material and weight. This is especially important if you’re 3-D printing for biomedical purposes, such as bone or joint replacements, or aerospace, where excess material means the difference between flying and not flying.
The high cost of additive-manufactured parts limits their applications in other industries, however there are reasons one may consider them. Wherever excess weight hurts the efficiency of a process, a strong lightweight part can help. The resilience of 3-D printed parts is also desirable where the cost of frequent maintenance, downtime and part replacements affect the bottom line.
Weld-less designs produced by additive manufacturing are another advantage. Equipment that once required multiple components to be assembled can be reduced to a single part, improving fatigue life and eliminating the need for rewelding. They can also be designed to serve multiple purposes at once, making former components obsolete.
Optimization can lead to the development of new high-performance parts, or retrofitted upgrades on older machines. However, it takes specialized knowledge to understand how each additive manufacturing method affects the build integrity of parts, and which method and material is best suited for its intended purpose.
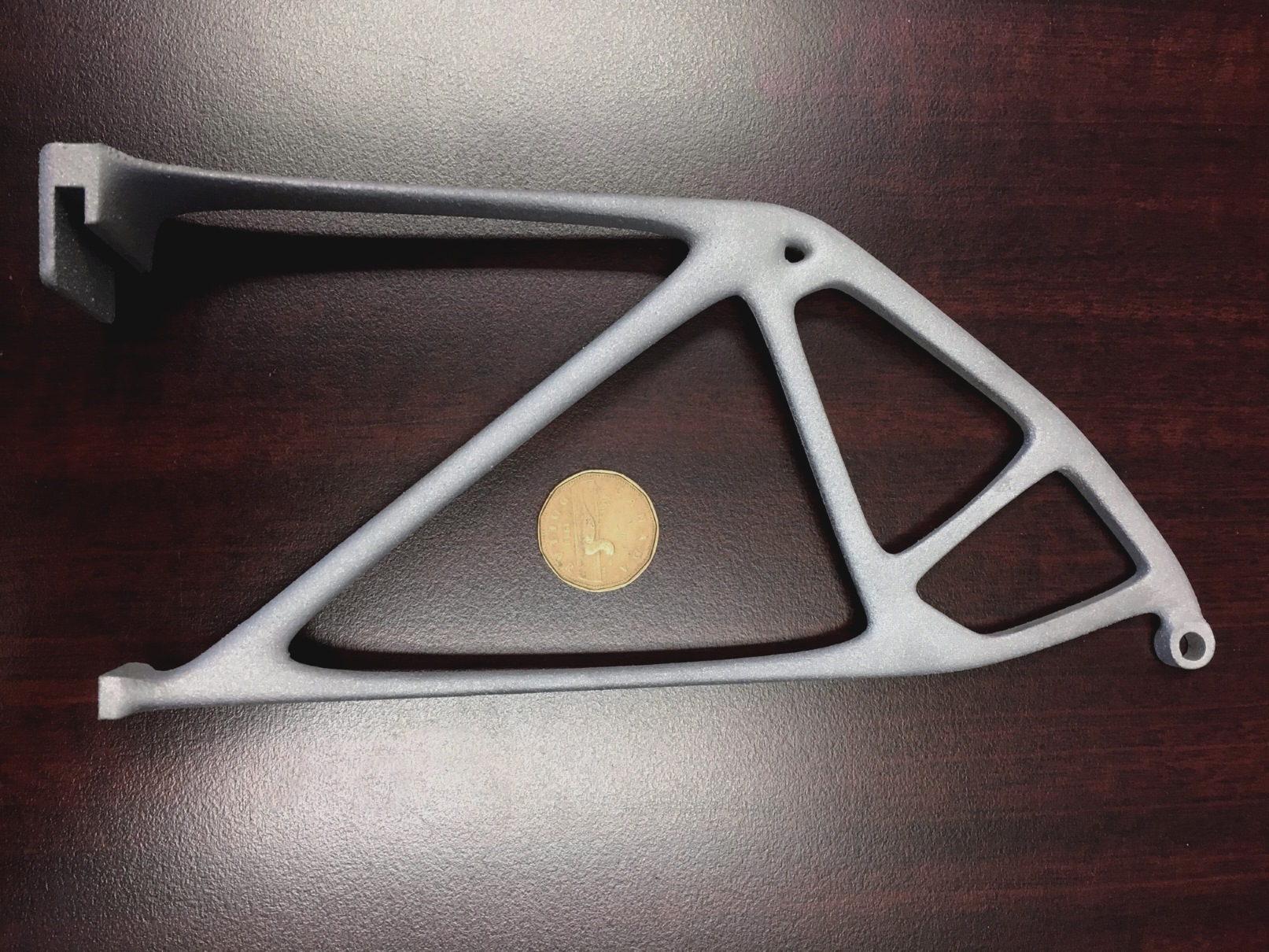
What ways are there to ensure 3-D printed parts or upgrades are fit for industrial use?
Despite the technology for 3-D printing being around for a long time, the software for optimizing parts is relatively new. This has created a knowledge gap among engineers who may lack training with the relevant tools and programs, but another constraint is the equipment required to develop and validate designs.
Additive manufacturing shows promise for retrofitting high-performance parts, but to do so, the old part must serve as a sort of template. A 3-D scanner can take objects from real life and digitize them as 3-D models. Engineers can use these models to define spatial constraints and connection points with other parts and loads. Using design software allows the engineer to perform a stress analysis and apply optimization, essentially reverse-engineering the part to build something new.
Examples of this are topology optimization—the process of removing all non-load-carrying material—and cellular lattice-based optimization, which hollows out solid material and replaces the internal structure with a skeletal web of lattice shapes.
Quality assurance is the next step. Since additive manufacturing may cause material imperfections within the parts it builds, a quick look-over is not enough to ensure integrity. Computed-tomography (CT) scan is one solution: an industrial CT scanner uses X-rays to capture a series of 2-D cross-sections and stitches them together to form a highly detailed 3-D image. This allows engineers to perform a material inspection and verify quality without destroying the part.
The remaining challenge for experts is identifying industrial processes where 3-D printed parts offer the most benefit for their cost. Additive manufacturing may be of niche interest to industry, but for broader applications, there’s value in deconstructing processes and re-evaluating them through the perspective design freedom provides.
Learn more about SRC's Industrial Engineering services.