This article first appeared on Energy and Mines.
There are several off-grid communities and industrial sites in Saskatchewan that use diesel generators to meet their electrical power needs. Generally these systems are able to perform their basic function and provide reliable power. However, they present some challenges as well. Fuel costs make up the bulk of operational expenditures for these systems. There are also financial and environmental risks associated with the transport and storage of this fuel. These costs and risks increase with the size of the site, as well as the level of difficulty involved with accessing the site. A generator, by principle, follows the electrical load, which leads to inefficiencies as the engine operates outside of its optimal range. This results in excessive fuel consumption, increased pollution and more frequent maintenance.
The need to improve overall efficiency of power generation has become a priority, especially as fuel prices increase and as mine development expands into more remote locations. Such a need was identified at one of the mine sites we're remediating, the former Gunnar uranium mine and mill site, as part of Project CLEANS (Cleanup of Abandoned Northern Sites).
Project CLEANS involves remediating 37 abandoned uranium mine and mill sites in northern Saskatchewan. An operating camp has been established at Gunnar, which is located on the north shore of Lake Athabasca.

Site Assessment
The camp operates during the summer months and accommodates up to 100 people. All the power needs for the camp were met by two legacy 500-kW generators, which were sized to meet the requirements of the initial demolition phase of the remediation effort, but were oversized for current operation at the camp. Diesel represented a major operating expense for the camp, as approximately 460 L/day of diesel was consumed to support the small camp. The fuel cost is approximately $2.30/L, including delivery to the site from the nearest bulk fuel station.
Diesel, Renewables and Energy Storage
To reduce the diesel consumption for the Gunnar camp, SRC developed the Hybrid Energy Container power system. SRC conducted extensive site monitoring of the camp to characterize the site’s load and then designed the customized hybrid system to maximize the fuel savings over the life of the remediation effort. All aspects, including battery chemistry, inverter technology, generator type and hybrid construction, were considered. It was constructed in the spring of 2015, received certification and was then transported from Saskatoon to the Gunnar camp via truck and barge.
The customized containerized power system has been integrated into a single modular container, which accommodates a generator, a battery, a photovoltaic array and an inverter system equipped with remote control and monitoring systems. This design makes the power system portable and rugged, while allowing multiple systems to be stacked to achieve higher generation and storage capacities, as well as to increase reliability through redundancy.
Hybrid Energy Container Features:
- Peak output capacity: 69 kW
- 60 kW diesel generator with 42 kW/259 kWh energy storage system
- 20-foot modular container, climate controlled, remotely operated
- Easily integrated into existing site infrastructure
Throughout the first summer of operation, the Hybrid Energy Container met all SRC’s goals by reducing diesel fuel costs, providing reliable power and reducing overall maintenance. The system is fully automated and can be monitored and controlled remotely.
During operation at Gunnar, the power system reduced generator runtime by over 70%, and is expected to save 86% of the site’s fuel consumption, providing approximately CAD$93,000 in savings during its first four months of operation and a payback period of less than 12 months of operation.
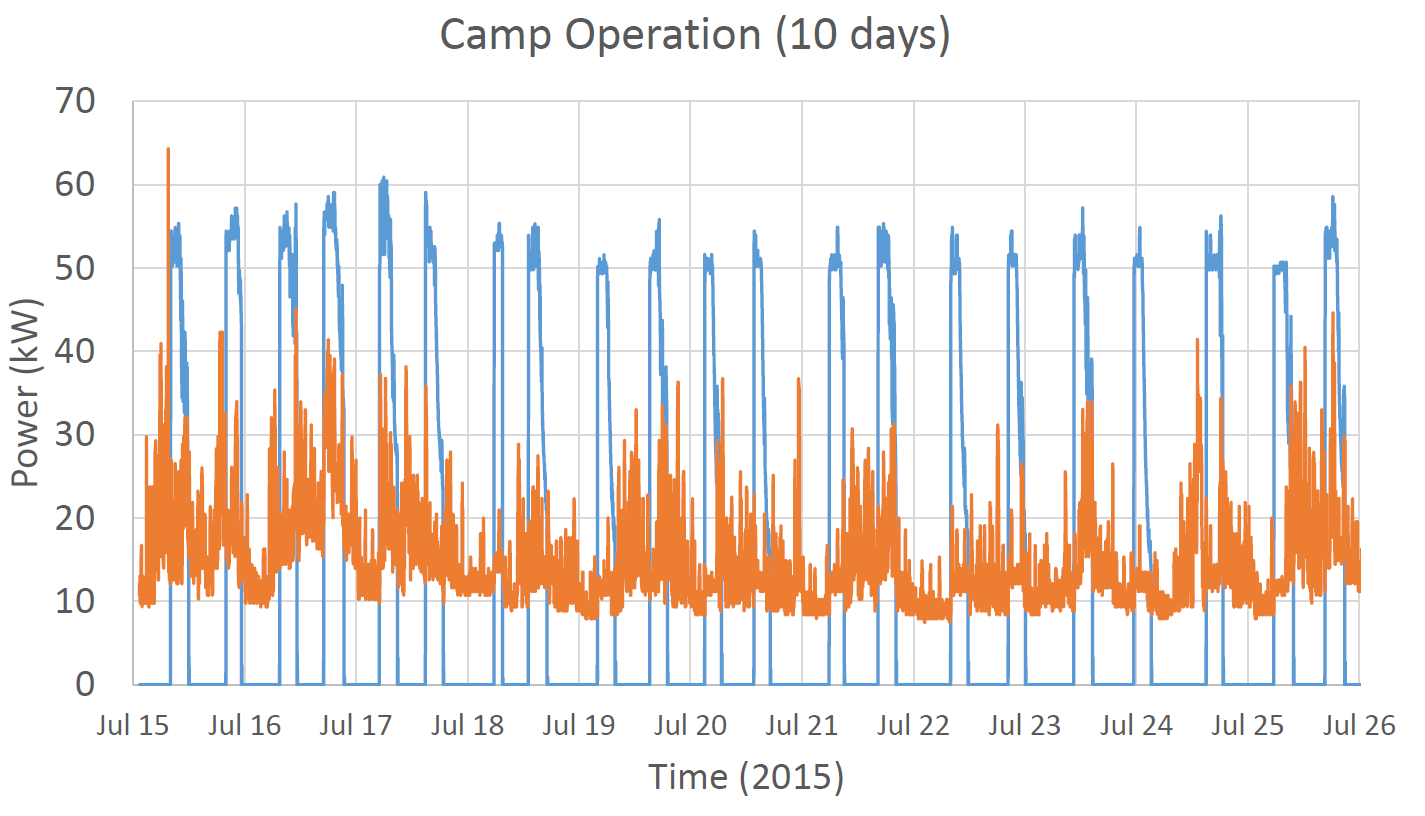
The Hybrid Energy Container has proven it can provide reliable energy to remote off-grid industrial sites and communities, while reducing fuel consumption and maintenance requirements. The system can also be customized and scaled to accommodate much larger loads at other potential sites. SRC is continuing to provide services and customized Hybrid Energy Container power systems to sites that benefit from the implementation of this technology.