This blog post is part of our Diamond Webinar Series with CIM Magazine. View the magnetic separation webinar and white paper to dive deeper into this topic. Sign up now to be notified of the next webinar.
Older, simpler technologies are often overlooked for their shinier, more sophisticated successors. Magnetic separation is one such technology, but give it a second look and you'll see it has many advantages that could improve mineral processing, such as its ability to handle high throughputs and easy operability. It’s also relatively low cost and reduces processing footprints downstream. Processing plants could capitalize on such technologies with some additional research.
As with any plant process, it’s important to understand the theory behind the method, as well as how to apply it in a way that creates efficiencies and reduces costs. When done correctly, magnetic separation is a simple, inexpensive method to recover minerals from host ore or remove waste from ore streams before further processing.
The information below draws from experiences at SRC’s Geoanalytical Laboratories’ Diamond Laboratory, but these processes also apply to other commodities.
A Brief History on Diamonds
Diamonds are brought to the earth’s surface through volcanic eruptions and are deposited in volcanic pipes known as primary diamond deposits.
In the last couple decades, diamonds have been discovered in various types of deposits (e.g., kimberlite, lamproites). These sources have a variety of other minerals present, which increases processing complexity because comminution parameters specific to each ore are required for liberation, and mineral variety increases the sorting criteria for the final diamond concentration.
Diamond Processing
Density separation is the easiest and most economical method of concentrating diamonds and for other commodities, as well.
The Dense Media Separation (DMS) concentrate contains a high percentage of magnetic minerals (between 20-80 per cent). Magnetic separation following DMS is an effective and inexpensive method to reduce the DMS concentrate prior to final recovery processes. It reduces the number of X-ray machines, grease or flotation recovery units and hand sorters required for downstream processing.
Magnetic Susceptibility
Kimberlite and other minerals have a range of magnetic properties, such as diamagnetic (quartz, diamond and zircon) and paramagnetic (chrome diopside and garnet) to ferro- (cobalt, nickel and iron) and ferrimagnetic (ilmenite and magnetite) that can be used to improve diamond recovery.
Knowing what magnetic properties your minerals contain allows you to more effectively design processes and setup equipment to further concentrate the feed or to remove waste streams earlier in the process.
Magnetic susceptibility, a key parameter to the viability of magnetic separation, is a measure of how susceptible a mineral is to a magnetic field.
The higher the magnetic susceptibility, the stronger the force of attraction to a magnetic field. A negative magnetic susceptibility implies the mineral is repelled by a magnetic force.
Strongly magnetic minerals are either called ferromagnetic or ferrimagnetic. The main difference between ferro- and ferrimagnetic is the curie point - the temperature at which the material loses all its magnetism. The curie point is a little bit lower in ferrimagnetic minerals.
Paramagnetic minerals have much lower magnetic susceptibility than ferro and ferrimagnetic. They are often overlooked and can easily be sorted if you have strong magnets. The recovery of these minerals can add additional revenue to the project.
Diamagnetic minerals have negative magnetic susceptibility and are repelled by a magnet when processed by a magnetic separator.
Magnetic Characterization of DMS concentrate
Before you use a magnetic sorter, you need to measure the magnetic susceptibility of the minerals in the DMS concentrate to determine their magnetic properties. This information helps determine the magnetic cut-point(s) in order to optimize your magnetic separation equipment prior to final recovery.
Magnetic susceptibility measurements are carried out with a magnetic susceptibility meter, also known as a kappabridge, which tells you how susceptible a particle is to magnetization. The kappabridge measures both weak magnetic forces (diamagnetism and paramagnetism), as well as strong magnetic forces (ferromagnetism and ferrimagnetism).
Understanding the magnetic susceptibility of the industrial and included diamonds to be sorted is imperative to optimizing the magnetic cut-point for minimizing yield on the magnetic separator and maximizing the economic value of a deposit.
The optimum magnetic cut-point for processing the DMS concentrate varies with each deposit and with the mining plan, since it is dependent on both the gangue minerals and the diamonds residing in the host ore.
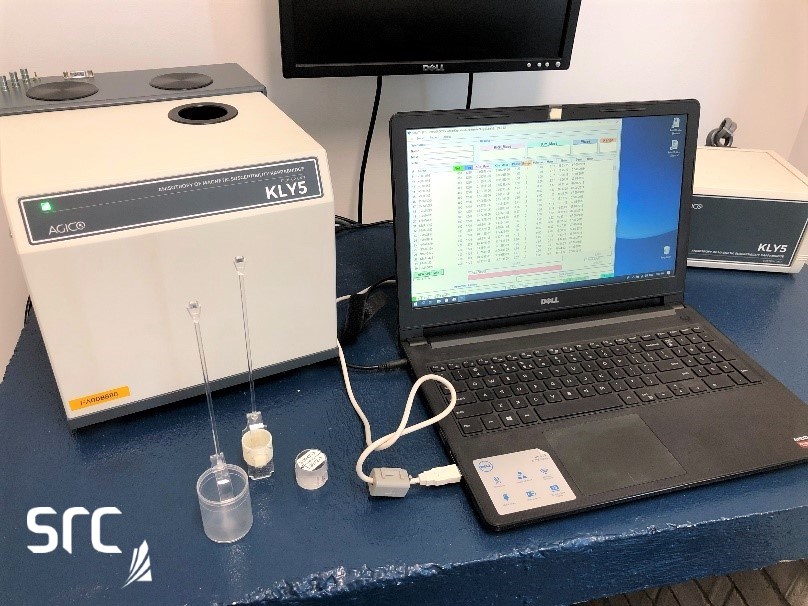
Magnetic Sorters and Applications
Magnetic sorting is inexpensive, relatively safe and has a high processing capacity. Once you know the magnetic properties your minerals contain, you can start determining what magnetic sorting equipment is required for your plant.
There are a variety of magnetic sorters with a wide range of magnetic field strengths for numerous applications in a processing plant. They’re used extensively in iron ore processing, but they also have a critical place in diamond processing plants and application in other commodities, as well. They can assist with tramp iron removal, waste removal from the DMS concentrate for downstream processes, recovering additional valuable minerals occurring with the diamonds (e.g., magnetite and garnets) and hand sorting to improve sorting efficiencies.
In your flow sheet, your low-strength magnetic separator comes before any high-strength magnetic separator because you want to pull off your ferro- or ferrimagnetic (i.e., ferrous) material first, otherwise it will stick to the magnet and you won’t be able to remove it from the high-strength magnetic separator and your equipment will experience high wear.
If your DMS concentrate contains weakly paramagnetic and diamagnetic minerals (e.g, diamonds), a three-stage tiered magnetic separation process is ideal for sorting.
- Stage 1: A weak magnet and a high-belt speed – scalping process removes ferromagnetic material
- Stage 2: A medium-strength magnet and/or slower belt speed – removes strongly paramagnetic minerals
- Stage 3: A stronger magnet with a slow belt speed – separates the weakly paramagnetic and diamagnetic minerals
On the other hand, if your DMS concentrate contains ferro- and ferrimagnetic minerals from an ore feed or slurry, one-stage magnetic separators are used, which incorporate only a weak magnet.
Inside SRC’s Diamond Lab
At SRC, our setup is unique as we have several different magnetic separators, which allows us greater flexibility in the services we offer to clients.
We use a high-throughput, one-stage magnetic separator with a very broadband magnet (approximately two-feet long). With different belt speeds, we can setup different magnetic cut-points.
We also have a laboratory permroll that does small batches, but the magnetic roll is replaceable so we can switch it out for a high-intensity magnetic roll or a low-intensity magnetic roll, depending on our client’s requirements. It’s important that the material goes over the magnetic field in a monolayer so there’s no impingement on the mineral separation.
We also have a two-stage magnetic separator in our plant, which is similar to a three-stage separator. In the two-stage, you typically have the weaker magnet at the top to separate your ferrous material and the stronger magnet at the bottom to separate your paramagnetic material.
We also use a wet magnetic separator in our plant to recover ferrosilicon (FeSi) used in the DMS and recycle it, as FeSi costs can be quite expensive. Recycling helps to minimize plant operating costs.
Calibrating a magnetic separator
Magnetic tracers are simulated diamonds of varying magnetic susceptibilities, which help to calibrate magnetic separators and identify operational parameters.
Running a series of magnetic tracer tests with different size fractions and/or with different belt speeds calibrates the magnetic separator for various operating scenarios. These tests also ensure the magnetic separation equipment is functioning correctly. Tracer tests should be carried out regularly as part of a maintenance program.
Knowing the magnetic characteristics and identifying the required belt speed and splitter plate position for processing the various size fractions enables one to identify the optimum magnetic processing parameters. This set of magnetic parameters can then be referenced for each change in the mining plan with regular confirmation tests carried out using magnetic tracers.
Properly configured magnetic sorters placed in key locations in the diamond processing plant can improve diamond recovery, increase gangue removal, reduce the number of X-ray sorting units and reduce the plant’s footprint, while reducing costs.
Hysteresis
Another aspect of magnetism is hysteresis, which in this case is when a material is still magnetized even after the magnetic force has been removed. For example, you’ll see this if you drop some sewing pins and pick them up with a magnet. When you pull the pins off the magnet, they’ll still stick together. Removing the magnetism in the pins requires you to reverse that magnetic field.
Hysteresis is important for the mineral processing industry because when you recover your ferrosilicon, it still has a remnant magnetization. If you don’t de-gauss (remove the magnetism) before it goes into your magnetic separator, the viscosity of your concentrate stream will increase and your minerals won’t separate efficiently. You want to make sure that all your ferrous material in your medium is de-magnetized to minimize process inefficiencies.
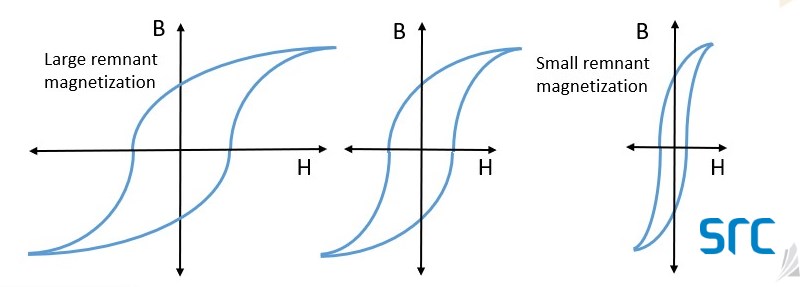
Designing A FlowSheet
When designing a flowsheet, you want to maximize separation as early as possible, looking at all the areas where magnetic separation can be used, and where it can be useful. They’re not always the same thing.
In a typical diamond beneficiation flowsheet, stockpile material should pass under an overband magnet to remove tramp iron before it goes into your DMS circuit where it can damage your equipment.
The material that is collected from the DMS is heavy and heavy minerals are often magnetic. Using a magnetic separator after your DMS can concentrate the material even further, between 20-80 per cent. This reduces the amount of material going to final recovery. Magnetic characterization of the DMS concentrate is required to optimize this process.
In final recovery, there’s often finer, high-tech equipment, such as X-ray machines, grease belt machines and laser-ramens. Reducing the material that goes through these machines means you can reduce the number of machines needed and the maintenance required, creating significant cost savings in the plant.
You can also look at using magnetic separation on your included and non-included stones in relation to creating efficiencies in hand sorting. It has been shown that it’s easier to pick included stones from a concentrate that has only paramagnetic minerals, and gem diamonds from diamagnetic minerals then it is to pick all diamonds from a concentrate that has both paramagnetic and diamagnetic minerals. Magnetic characterization of the diamonds is required to optimize this phase.
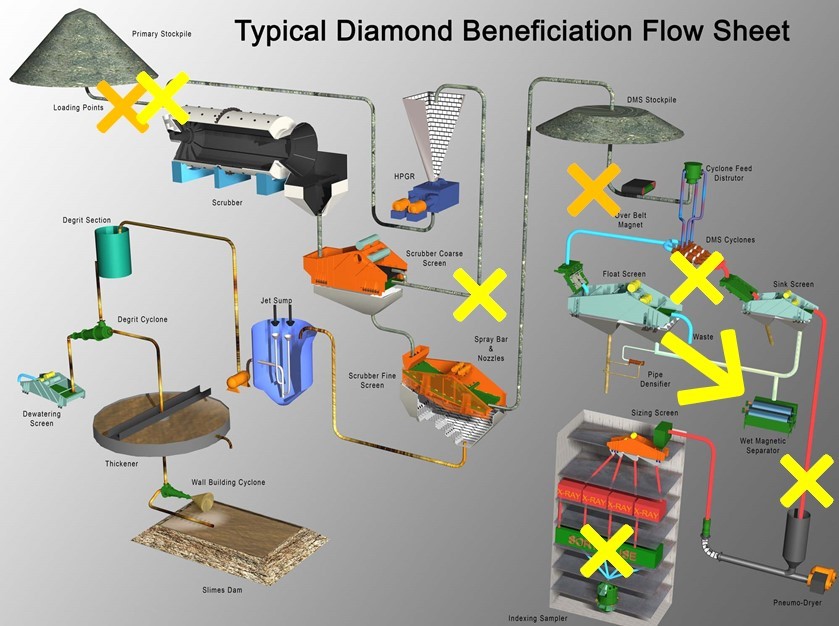
The Future of Magnetic Separation
In the last decade, magnetic separation technology has advanced as more rare earth elements are now incorporated into the manufacture of rare earth magnets.
With the development of magnetic tracers, we can now set up magnetic separators to separate minerals on a wide range of magnetic properties: from diamagnetic to weakly paramagnetic to strongly paramagnetic to weakly ferromagnetic to strongly ferromagnetic.
Magnetic separation is also used successfully to separate and recover valuable industrial minerals, as demonstrated by SRC’s Mineral Processing group who have done a lot of work in this area. The major cost of mining and recovery of these valuable industrial minerals has already been paid for as these minerals report with the diamonds in the DMS concentrate. Adding another recovery stream on the DMS tailings, incorporating additional magnetic separation to recover other valuable minerals as byproducts, would also increase revenue to the processing operation.
Magnetic separators have high-capacity, moderate footprints and consume relatively low energy. They offer a technological solution to more efficiently remove waste, concentrate ore and recover a range of valuable minerals.
Looking for help with magnetic separation?
For diamond and non-diamond applications, experts in SRC's Mining and Energy Division can help companies characterize their ore and minerals to determine their magnetic characteristics using a magnetic susceptibility metre (kappabridge). This helps determine whether magnetic sorting is a viable option. We can assist clients in setting up magnetic separator processes using magnetic tracers and their understanding of partition curves.
SRC can also provide guidance on the different types of magnetic sorters and, based on a plant’s requirements, assist in setting up or troubleshooting this equipment using an understanding of the ore, magnetic measurements and magnetic tracers.
Interested in learning more? Check out our on-demand Diamond Webinar Series.