Sensor-based sorting to remove waste—or upgrading ore prior to downstream metallurgical processing—is becoming more common in mining operations. There are many reasons to upgrade ore. The earlier you can get rid of undesired waste rock, the lower the cost and footprint of your downstream processing operations—including unnecessary transportation.
Removing waste and upgrading low-grade stockpiles can increase mine life and lower cut-off grades, and it can also give you the opportunity to manage material for reclamation and closure activities.
Sensor technologies, such as X-ray transmission (XRT), near infra-red (NIR), optical and laser, can instantly pick up mineralogical differences in solid ore particles. The new development over the last decade is that sensor instrumentation and data processing capabilities applied in various mining and processing operations, can now measure, process and evaluate in a manner of nanoseconds.
X-ray transmission (XRT) sorters are a popular choice for mineral processing plants due to their sorting ability, robustness and applicability across a variety of ores, but how can a mining company know if XRT is right for them?
SRC offers a unique test that combines high-resolution X-ray micro-Computed Tomography (CT) with Quantitative Evaluation of Materials by Scanning Electron Microscopy (QEMSCAN®) to obtain valuable information that can generate key data about your ore’s amenability to XRT sorting and streamline metallurgical testwork programs.
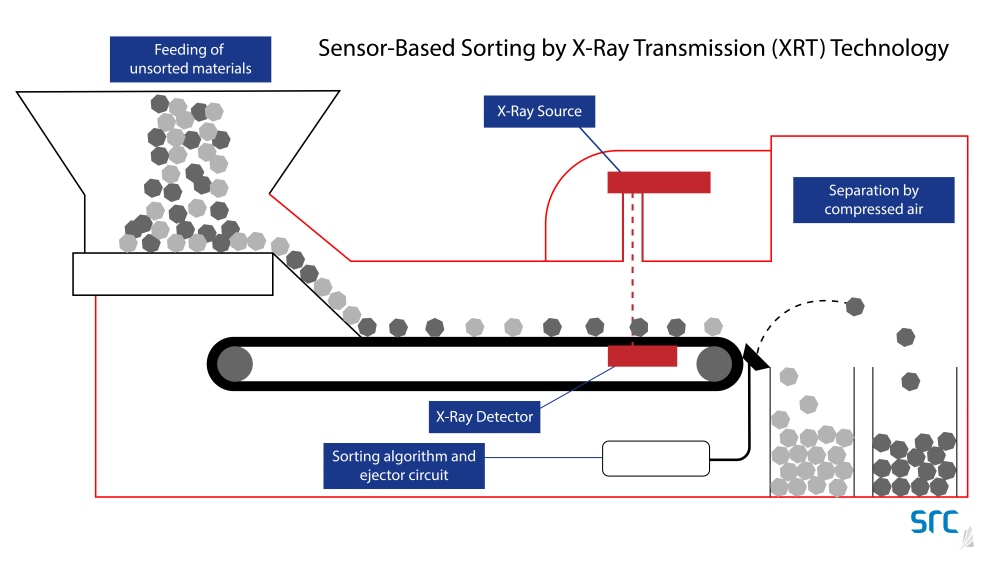
Today’s Testing Technology
Currently, XRT sorters pass high-intensity X-rays through particles to generate greyscale images based on effective atomic density. Using algorithms based on these images, the particle sorter (“ore sorter”) processes these images and is able to identify particles from each other, then mechanically separates them using air ejection mechanisms.
Current bench-scale tests provide empirical imaging information on the ore particles used to predict separation, but they do not provide an understanding of the actual mineralogical composition of the ore. SRC’s test does not replace the current technology—however, it allows for better application of it.
Furthermore, XRT technology lacks the ability to provide differentiation data on different minerals with similar atomic densities. The optimal particle size for sorting is a function of the ore’s mineralization, the commodity being extracted and the sensitivity of the sensor used in the sorting equipment.
3-D computed tomography (CT) volume image and its corresponding 2-D projection images of rare earth ores.
Advancing the Idea
SRC’s team conducts 3-D CT scanning on samples to obtain volumetric information of individual mineral phases. QEMSCAN® is then used to calibrate the greyscale values of the 3-D volume, which reflects different atomic numbers of minerals in the samples. The test also provides information about particle thickness, desired mineral presence and mineralogical information regarding associated minerals and clays to assist with developing sorting algorithms.
“Mineralogy information from QEMSCAN® can identify incidences of mineral encapsulation, problematic clays and detrimental minerals, as well as calibrate the greyscale values of CT data for optimum algorithm development. Plus, additional 3-D CT imaging on cores provides spatial information of the minerals within the ore and mineral grades,” says Jane Danoczi, Senior Process Engineer, Process Development at SRC.
What it Means
“Combining CT and QEMSCAN addresses the many limitations of the current way to determine whether XRT sorting technology is appropriate for ores,” says Peng Luo, SRC R & D Technical Advisor, EOR and In-Situ Processes.
“These together can form a unique dataset that helps to characterize the formation and optimize the extraction process for minerals that no other test is able to do.”
Highly valuable to industry, this test has many uses, such as:
- Core digitization for core logging and profiling
- Measuring spatial information such as grade, grain size distribution, surface contact areas between minerals
- Helping, together with minerals processing tests, to optimize processing parameters where ore sorting is used; and
- Monitoring dynamic processes, such as solution mining and geomechanical tests.
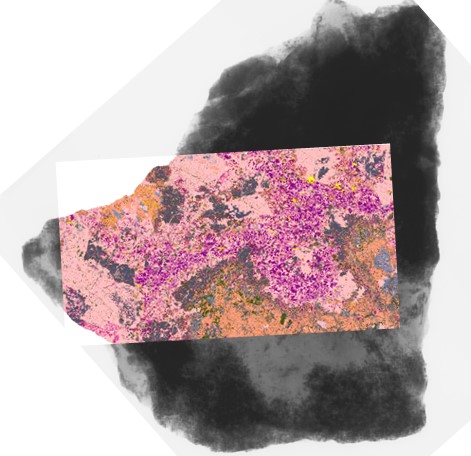
Perhaps most importantly, this is a non-destructive test. It does not need special sample preparation; it is flexible in sample geometry and size and samples can be scanned at extremely high resolution.
“By using a combination of 2-D CT, 3-D CT and QEMSCAN® technologies, an ore’s amenability to XRT sorting can be fully investigated very early on in any mining project,” says Luo. Important sorting parameters such as sorting size, size ratio, resolution requirements for possible belt speed and throughput tolerances can be identified.
Plus, you can determine whether sorting can occur directly by detecting the commodity or by detecting an associated mineral or by detecting the barren ore for removal (waste removal).
“Sorting has proved invaluable in urban waste sorting, recycling and the food industry,” says Danoczi.
“Mining is now seeing the benefits of sorting," she continues. "By processing only ore that needs to be processed saves on energy, chemicals, water and the size of the mine. Looking forward, sensor-based sorting will enable the mining of the sea floor bringing only the valuable ore to the surface or the mining of asteroids returning only the valuable ore to earth.”
Interesting in learning more about SRC’s sensor-based sorting characterization work? We co-hosted a two-part webinar series with CIM Magazine that is available on demand.
This post was written by Brook Thalgott, a former SRC employee.