This post was written by former SRC employee Ralph Jonasson.
When constructing industrial plants (e.g., storages vessels, reactor vessels, plumbing and sensors), the selection of materials is part of the cost equation. Metal alloys should ideally be inexpensive and easy to work with. But when metals wear out too quickly, it’s not only an issue of replacement cost and downtime, it’s a question of safety.
Many industries in western Canada face corrosion problems due to the frequent exposure of metal alloys to water, salt, oxygen, carbon dioxide, hydrogen sulfide and lesser well-known sulfur compounds.
Low carbon steels are often used in pipes and vessels because they are strong and inexpensive. Their welding properties are also well known. But when exposed to oilfield fluids high in carbon dioxide (CO2) and hydrogen sulfide (H2S), these steels tend to dissolve, reducing their strength, and they become coated with corrosion products: iron oxides (like FeOOH, Fe2O3, Fe3O4), carbonates (FeCO3) and sulfides (FeS, FeS2). These corrosion deposits can restrict flow and flake off and contaminate other systems.
In potash production, metals can be exposed to very concentrated brines containing sodium chloride (NaCl) and potassium chloride (KCl), whose attack on these metals is enhanced by air, CO2 or H2S.
Where corrosion rates are too high, companies are sometimes forced to replace less expensive steels with alloyed steels, such as various stainless steels, which contain at least 11.5 weight % chromium, by definition. If even these materials fail, more exotic metals are used, such as Hastelloy C276 (a nickel alloy) or titanium or titanium alloys.
Hastelloy is just as strong as low carbon steel over a wide temperature range, but titanium loses strength quickly with increasing temperatures. Titanium alloys are also softer than carbon steels and stainless steels. The situation is made worse by the fact that many standard valves, pipes, tubing and fittings are not available in exotic materials.
Therefore, it’s necessary to test materials under conditions that closely replicate the application environment. Although attempts have been made, there is no simple equation that can predict under which conditions a particular alloy will fail at a particular rate.
Inside the Lab: Test 1 – H2S From Elemental Sulfur
At SRC, we’ve started preliminary work on developing relatively simple “jar tests,” using 0.5 L pressurized vessels, to test metal alloy samples (i.e., “coupons”) under specific conditions, such as steam-assisted gravity drainage oil production or potash solution mining. In both cases, sulfur was an element we specifically targeted.
Sulfur is a comparatively reactive substance, especially in the presence of water, and at higher temperatures. Simply heating sulfur and water will cause it to disproportionate into H2S plus SO2. When organic substances are present, the SO2 oxidizes the organic matter to generate more H2S. This is important to know in tracking sources of H2S. This reaction is favoured by high pHs, as shown in Figure 1.
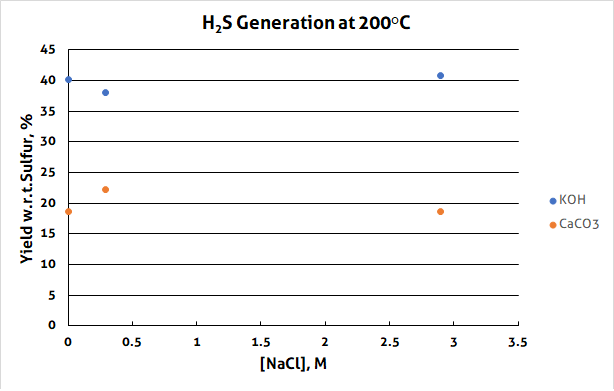
Inside the Lab: Test 2 – Sodium Chloride and Ammonium Sulfide
In another test, four metal coupons were reacted with an aqueous solution containing 10 weight % NaCl and 0.01 weight % ammonium sulfide at 106°C and 950 kPa CO2 for one week. Pressure vessels lined with Teflon were used to prevent corrosion of the containment vessels themselves. Figure 2 is a photograph of the four metal coupons, along with some of the corrosion products.
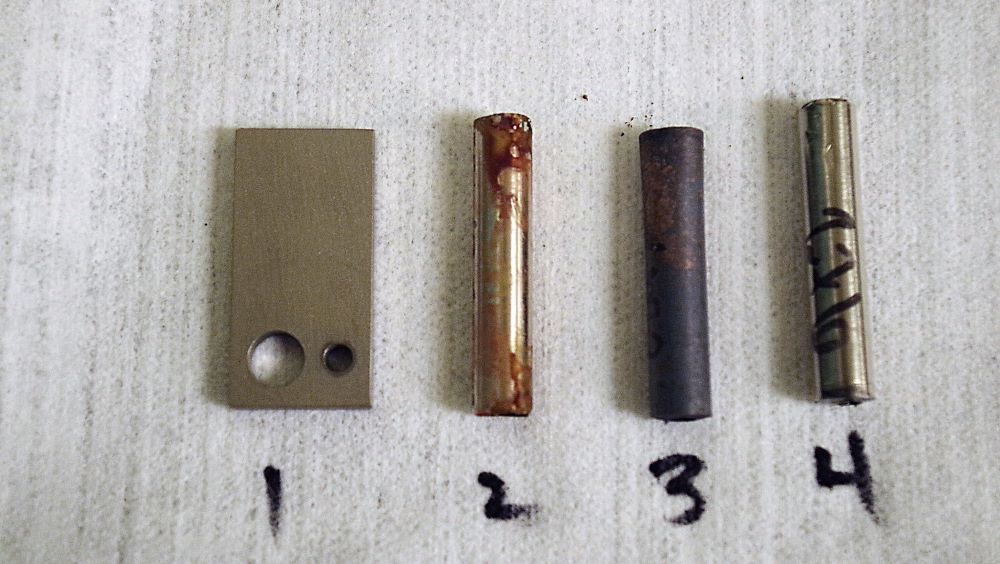
1. Titanium (grade 5)
2. 316 stainless steel
3. Monel (Cu/Ni alloy)
4. Hastelloy 276 (Ni/Cr alloy)
In Figure 3, you can see the weight lost by each coupon after the test. In this test, the titanium alloy performed the best. Standard tubes and fitting are commercially available in all the materials tested, but they are much more expensive than 316 stainless steel, which is one of the more frequently used materials. Many tradespeople are familiar with 316 stainless steel, so they are reluctant to try alternatives. This is why it’s important to have research labs that can provide objective testing, customized to specific applications in a field operation or production plant.
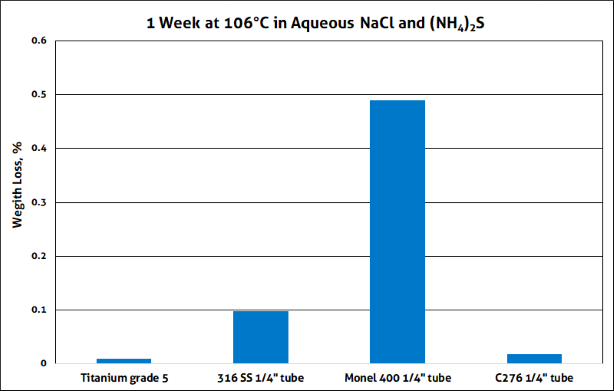
More Testing is Needed
The study of metal corrosion has been around for centuries. There are professional societies that focus on corrosion research and testing, provide standards and make recommendations to industry. The companies that make metal alloys, and the companies that manufacture products such as sheets, pipes, fittings, valves and pressure vessels also provide information about corrosion to customers. There is a wealth of information out there.
However, specific applications sometimes require specific testing. At the moment, there is no perfect material, so the search for new materials, surface coatings and corrosion inhibitors continues.