SRC offers comprehensive sensor-based sorting (SBS) design and testing services across the entire process, from mineralogical characterization to pilot testing. Our expertise spans a range of ore types and sensor technologies, such as X-ray transmission (XRT), electromagnetic and laser scattering, ensuring clients are recommended the optimal sorting technology selection for their operation.
SBS technologies are changing how the mining industry is evaluating mine design and economics. Sorting can remove waste and upgrade marginal deposits, which can increase mine life and lower cut-off grades. Advances in sensor instrumentation, processing capabilities and artificial intelligence have enhanced the ability to measure, process and evaluate ore within nanoseconds.
Testing Stages for Sensor-Based Sorting
SRC's testing regime assists in choosing the right sensor-based sorting technology for their needs.
Learn about the different stages, from mineral characterization through to pilot-scale testing.
Get the Latest News
Interested in learning more about our mining services and hearing about upcoming events with our experts? Subscribe to receive our newsletter.
The SRC advantage
SRC’s experts apply their understanding of sensor performance, mineral characterization and processing to help assess the viability of all sorting options, providing a third-party, independent evaluation. This information can be used to assess the potential of both bulk and particle sorting.
We can test all major sorting technologies on the market and have developed custom-made, sensor-based solutions for various applications. We offer SBS process development, testing and piloting as part of our full suite of mining services.
Our detailed analyses and reports are suitable for use in technical and financial assessments, ensuring compliance with industry standards. This independent and professional approach guarantees accurate, reliable data that can be confidently used for making informed decisions about ore processing and mine development.
Benefits and Applications of Sensor-Based Sorting
SBS technologies are widely used in various sectors, including recycling, food and mining industries. Their application in greenfield mining projects can significantly reduce energy costs, minimize waste and lower the environmental impact by decreasing tailings and improving ore processing efficiency.
SRC’s interdisciplinary team, comprising geologists, mineralogists and engineers, ensures a complete approach to SBS technology integration, making it a reliable partner for mining companies looking to adopt these advanced sorting solutions. Our focus on sustainability and operational efficiency aligns with the latest industry trends and regulatory requirements.
- Increased Efficiency: SBS can separate ore from waste based on mineralogical differences detected by sensors.
- Reduced Waste: By removing waste rock as early as possible in a flowsheet, SBS technology improves the efficiency of downstream processing, reducing energy and water use in greenfield projects.
- Environmental Impact: Reducing the amount of material processed decreases the environmental footprint of mining operations by reducing energy consumption and emissions. Sorting also reduces the need for chemicals at this stage, allowing for a dry processing method that minimizes environmental impact.
- Improved Safety: In some flowsheets there is a need for manual sorting; replacing this step with SBS technology can enhance safety.
- Operational Cost Reduction: By optimizing the process, SBS may lead to significant cost savings.
Types of Ore Sorting
There are two major types of sensor-based sorting: bulk sorting and particle sorting.
- Bulk Sorting: Uses sensors on mine equipment or conveyor belts to identify and divert waste rock sections (bulk “parcels”) usually from run-of-mine ore, ensuring only certain mineralized ore reaches processing plants
- Particle Sorting: Sensors identify differences at the particle level within crushed ore, separating high-gangue content from higher mineral content particles
Testing Stages for Sensor-Based Sorting
SRC's comprehensive three-stage testing regime assists in selecting the most appropriate SBS technology, progressing from mineral characterization to targeting and modelling and then to pilot-scale testing.
Stage 1: Sensor-Based Mineralogical Characterization
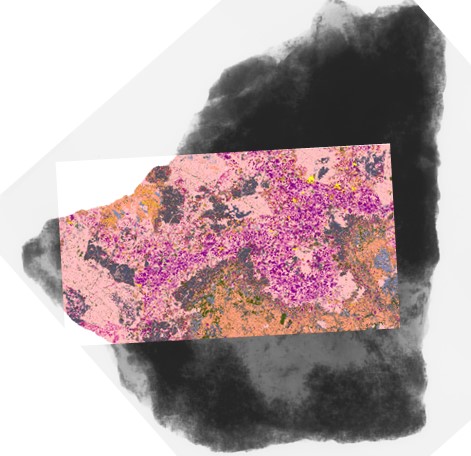
- This initial stage assesses ore amenability to SBS technologies, such as X-ray transmission (XRT), near infra-red (NIR) and laser scattering.
- QEMSCAN® analysis is used to provide critical data on the modal mineralogy and grain size of the deposit. This helps identify the ore minerals present, as well as any penalty minerals.
- These tests provide important information on upgrading potential and reference parameters for sorting equipment and processing.
This stage uses sensors to identify and measure mineral properties and determine how different sensors respond to the mineralogical composition. Detailed knowledge of the ore’s properties is crucial to ensuring the sorter can be calibrated for the best results.
Stage 2: Targeting and Modelling
- Through client discussions, the optimal sorting strategy, including sensor type and target mineral, is determined.
- Static tests are conducted, with the sensor responses of individual particles being gathered and correlated to QEMSCAN® mineralogy.
- Small, dynamic cascade tests are run based on the findings of the static tests to develop an ideal baseline sort.
Stage 3: Pilot Testing
- This stage refines algorithms and assesses sorting yields, recoveries and overall circuit performance.
- Testing is carried out on run-of-mine material at full production capacity.
- Provides crucial data for evaluating the feasibility of a sorting project.
Particle Sorting Equipment Technologies
At SRC, we can provide amenability information for a wide range of sensor and detector technologies, as well as batch and bulk-scale testwork:
- X-ray transmission (XRT): Two dual-energy XRT industrial sorters that run at full production capacity and are used for bench and pilot-scale testing
- Electromagnetic induction (EM): Integrated into one of the full-scale, dual-energy XRT sorters is an EM sensor bar, used for bench and pilot-scale testing
- Laser scattering: Initial testwork for laser sorting amenability
- X-Ray induced luminescence (XRL): Amenability, bench and pilot-scale XRL testing
- Ultra-Violet (UV): Initial testwork for UV sorting amenability
- Near-infrared (NIR): Initial testwork for NIR sorting amenability
- Colour: Initial testwork for colour sorting amenability
Future Developments
SRC is continually advancing its SBS technologies to stay at the forefront of the industry. We are excited to announce the upcoming addition of a full-scale laser sorting unit, expected to be operational in fall 2024. This new technology will further enhance our capability to deliver efficient, cost-effective and sustainable sorting solutions.
Contact us to discuss how our experts can help your operation select and test the most appropriate SBS technology.